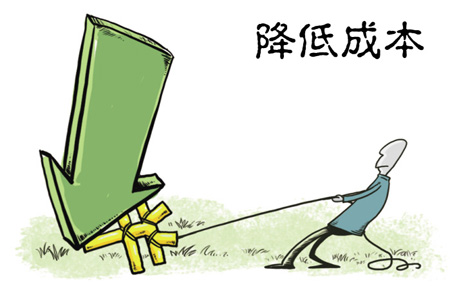
For these problems, combined with the real-world approach, take a hardware factory as an example to see how the author resolved:
1. A hardware processing factory that is generally composed of a mold department, a manufacturing department, a surface treatment department, an assembly department or an assembly department, and some management departments (personnel, business, finance, information, sales, etc.). In these departments, the mold department and the manufacturing department are the key departments (general mold department is assigned to the technical center, and the technical center is mainly responsible for technological issues such as process editing and mold design and related products). Why is it a key department because of the cost they occupy? It is the largest cost to occupy, which accounts for almost 70%-90% of a product's cost. Therefore, how to control the cost is to start from the technical aspect. The significance of controlling employees' wages is not great, and the salary of employees is also based on local The level of work is not given willingly, so the wages of employees change again. For a small company, one person has 150 more a month, and if it counts as 500 people, it is only 75,000. Seventy-five thousand are only the cost of a set of molds, so to improve profit, we must strive for technology.
2, there is a sample and product manufacturing cycle is also a key to the cost of the key, the shorter the sample period can reflect the company's strength is better, it will be easier for customers to place orders, it is easy to make money. The production cycle of samples or products is composed of various departments, not a single department, so all departments must cooperate with each other to achieve a short production cycle. The production cycle has a direct relationship with the mold making cycle. Even the time for mold making takes up more than 60% of the entire sample production time, so controlling the time of the mold is also a strategy to reduce costs.
For these kinds of issues, several major issues can be summarized: the quality of the mold, the coordination of the department, the strength of the company, the quality of the product, and the production time of the product.
How to solve these problems?
1, for the quality of the mold. The quality of the mold is a good or bad product, so in order to achieve a successful mold test and reduce the cost of waste, the company needs to introduce new technologies to improve this problem. For the hardware factory, the mold forming method is generally casting and cold punching, so the mold flow software can be introduced to analyze the rationality of the mold design and whether there is a product defect.
Through the calculation and analysis to rectify the defects, and finally achieve the goal of a successful test mode, thereby greatly reducing the cost of mold repair and shorten the mold debugging and production cycle. Once the problem of the mold was solved, it basically solved the cost reduction of 70% to 85%.
2. The problem of cooperation between departments is generally a matter of cooperation between the technical department and the manufacturing department. If the mismatch is between the two departments, the sample will be difficult to make, thus increasing the production cycle and increasing the cost. Therefore, to solve the problem of cooperation among departments, it is possible to make the sample production smoothly without any obstacles. It is a supervisor of a department and can be changed into a supervisor of two departments. After adjustment of the organizational structure, the sample production will be much smoother. To achieve the reduction of manpower and material costs.
3, the company's strength is generally through packaging, packaging itself is also a means of business strategy, as long as each time a guest to visit, the company will arrange, put a variety of new technologies and new software out to guests to visit, so that guests know the company's The strength is so strong that the price of making a product increases a bit, and guests have nothing to say. The price of the order given by the guest will be adjusted according to the strength of the company. Not all companies are the same.
4. The quality of the product, through the introduction of technology and quality control methods, the product's yield rate will increase, so the quality of the general comparison control, but also does not have a direct relationship with the cost reduction.
5, the product production cycle, with the production cycle of the product has a greater impact is the mold production cycle and product processing cycle. The processing cycle of the product has a lot to do with the cooperation and promotion of the department, so the problem of the production cycle of the mold and the cooperation of the department is solved. This problem can be easily solved.
6, the preparation of process flow. This point is very important. The rationality of process flow preparation directly affects the quality of the product, the use rate of the machine, the number of people operating the machine, and the production cycle of the product. Through the improvement of equipment, the introduction of equipment, and the introduction of new technologies, the process flow becomes simple, and even a single process can be completed to complete the entire product.
7. Through the introduction of informationization and the introduction of PDM or ERP, the data resources of various departments can be shared to achieve the purpose of accuracy, timeliness, automation and integrity, and the use and flow of personnel can also be reduced.
Through the above seven major improvement measures, the costs will be substantially reduced and profits will be made for themselves. With regard to rent, oil, and salt, raw materials have risen, and the cost of hydropower gasoline has not been controlled by the company. Moreover, those costs are not much, and the cost savings are not as good as the cost of two molds. With this change, the boss's problem does not exist.