Hydrogen as an environmentally friendly clean energy is considered to be an important alternative to fossil fuels. Photocatalytic decomposition of water to hydrogen is a promising green hydrogen production approach. A major factor affecting the efficiency of photocatalytic hydrogen production is the low separation efficiency of electrons and holes. The production of hydrogen or/and oxygen-producing additives (for example, Pt, Pd, CoOx, NiO) on the surface of semiconductor materials can effectively improve the separation efficiency of electrons and holes, especially for photocatalysts containing double adjuvants. The photocatalyst shows better catalytic performance. However, for most of the dual-agent photocatalysts, the additives are randomly distributed on the surface of the semiconductor material, which makes the direction of overflow of electrons and holes random, thereby increasing the recombination probability of electron holes.
In recent years, Atomic Layer Deposition (ALD) technology has attracted more and more attention from researchers in the field of catalysis. It shows outstanding advantages in the preparation of ultra-fine nanocatalysts, catalyst surface interface control, limited-domain catalysts, and multifunctional series catalysts (Angew. Chem. Int. Ed., 2015, 54, 9006-9100; Angew. Chem Int. Ed., 2016, 55, 7081-7085). Recently, the research team of the State Key Laboratory of Coal Conversion of the Institute of Coal Chemistry of the Chinese Academy of Sciences and the Research Team of the State Key Laboratory of Coal Conversion of the Chinese Academy of Sciences Yong Yong teamed up with researcher Zheng Zhanfeng to use ALD to design and prepare a porous TiO2 nanotube photocatalyst with spatially separated Pt and CoOx dual promoters. Using a carbon nano-helix (CNC) as a template, Pt nanoclusters/monoatomic and TiO2 layers were successively deposited on the surface of the CNC. After being calcined in the air, the CNC template was removed, and the amorphous TiO2 was crystallized and converted into a porous anatase TiO2 to obtain a porous TiO2/Pt photocatalyst. Then, ALD was used to deposit CoOx nanoclusters on the outer wall of TiO2 nanotubes. Finally, a porous TiO2 supported Pt and CoOx double additive CoOx/TiO2/Pt photocatalyst was obtained.
Under ultraviolet light, electrons and holes overflow to the Pt of the inner wall of the tube and the CoOx of the outer wall of the tube, respectively (the corresponding hydrogen-producing semi-reaction and methanol oxidation reaction occur respectively), thereby improving the separation efficiency of electrons and holes and corresponding The photocatalytic activity of hydrogen production. The results show that when the number of ALD deposition cycles of Pt and CoOx is 1 and the corresponding loadings are 0.046% and 0.019%, respectively, the prepared CoOx/TiO2/Pt has the best photocatalytic hydrogen production activity (275.9 μmol H-1) is 1.5 times (185.9 μmol h-1) of TiO2/Pt activity and 5 times (56.5 μmol h-1) of blank porous TiO2 nanotubes. In addition, the prepared space-assisted dual-assisted photocatalyst CoOx/TiO2/Pt was randomly distributed in the tube (TiO2/Pt-CoOx: 131.7 μmol h-1) and out of the tube (Pt-CoOx/TiO2: 73.7) The μmol h-1) catalyst also showed higher catalytic activity. The results were recently published in Angew. Chem. Int. Ed., 2017, 56, 816-820.
The method is universal and can be used to synthesize photocatalysts of other systems (for example, replacing CoOx with NiO, RuO2, MnOx, etc.), which provides an important scientific reference for the design and preparation of high-efficiency photocatalysts in the future.
The project received funding and support from the National Natural Science Foundation of China, the 100-person plan of the Chinese Academy of Sciences and the 100-person plan of Shanxi Province.
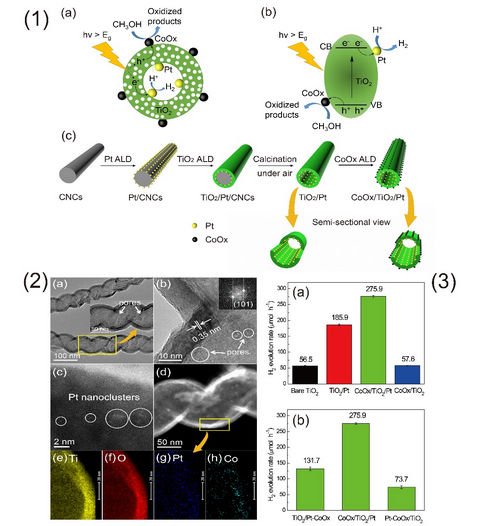
Resin Bond diamond and CBN Grinding Wheels
are made of either phenolic or polyimide resins. Pressure and heat are utilized
to bond the resin to our grinding wheel cores.
Phenolic bonded wheels can be utilized in dry or wet applications. Our
polyimide bonded wheels are best utilized in water or oil-based coolants for
improved form holding, typically required in CNC tool and cutter applications.
Resin bonded CBN Grinding Wheels are widely used on CNC machine for all tyeps of high speed steel cutter and drills machining and sharpening. They come mostly on shape of straight wheel of plat wheel, or bow shape wheel, or the working part can be sharpened to special shape like v shape or bevel shape.
A silicon carbide stone dresser is mostly used for the diamond or CBN grinding wheels.
Kemei produces all types and shapes diamond grinding wheels and CBN grinding wheels, and wheel dressers. If you need any grinding solution, contact us.
Resin Bond Grinding Wheels,Resin Bonded Diamond Wheel,Resin Bond Cutting Wheel,Resin Bond Diamond Cutting Wheel
Henan Jinlun Superhard Material Co., Ltd , https://www.jinlunsuperhard.com