There are many manufacturing methods for epoxy resin molding compounds, and they can be roughly classified into three types: premixing method, prepreg method, and extrusion method. These three types of methods naturally have their own advantages, strengths, and corresponding scope of application, but in the end, what are the advantages and disadvantages of each? According to the experts of China Epoxy Resin Industry Association, we have specifically explained the doubts.
The first method of manufacturing epoxy resin molding compounds is to pre-mix a fiber molding compound. The premixing method is to impregnate chopped fibers and fillers with epoxy resin glue, mix them evenly and then torlow and dry to obtain fiber molding plastics. The molding compound is characterized in that the fibers are loose and non-oriented, and the fluidity is good. The output can be large or small; but the specific volume is large, the fiber damage is large during the manufacturing process, the strength is lowered, and the working conditions are poor. Each process can be manually operated, suitable for small-scale production and trial production; it can also be mechanically operated, suitable for mass production, with less fiber damage and high product strength during manual operation.
The following points should be noted in the preparation process: First, the fibers should be treated with a reinforcing sizing agent, otherwise the paraffin sizing agent on the surface of the fiber should be removed by heat treatment to make the residual oil amount less than 0.3%, which is not only troublesome but also The fiber strength will be reduced, the fiber will be shortened, the length of the fiber during mechanical premixing will not exceed 20~40mm, the hand premix will not exceed 30~60mm, and the fiber will be fluffy; the second is to calculate the premixed material according to the formula. The amount of solvent is adjusted to have a suitable viscosity, so that there is no residual glue after the impregnation and mixing to ensure the plastic content of the molding compound. Generally, the viscosity is smaller when the temperature is high in summer, and the viscosity is low when the temperature is low in winter. To be larger; the third is the preparation of additives. Other solid additives should be ground, sieved, and dried to meet the specified specifications. Fourth, the impregnation and mixing should be such that the resin glue is fully impregnated with fibers and fillers and mixed evenly.æ‰, when the batch is large, the z-type kneading machine can be used; the fifth is to tear the loose, and the materials that are evenly mixed are torn and fluffed by hand or tearing machine, and the main machine is torn. The feeding roller and a pair of torn rollers with hook teeth are used to tear the fed mass through the reverse movement of the tearing roller; the sixth is to uniformly spread the loose premix to the clean metal. On the Internet, the layer should not be too thick (usually about 20 ~ 30mm), first cool at room temperature, and then most of the solvent is evaporated before drying and pre-polymerization to a certain extent, the oven temperature is 80 ° C, drying time 20~40min; Seven is the batch, packaged and baked molding compound should be quickly cooled and batched, and packaged in a plastic bag.
The second method is to prepare a fiber molding compound by a prepreg method, and the prepreg method is a method for manufacturing a fiber molding compound by a whole process of continuously splicing a continuous fiber bundle through a glue tank dipping, drying, and cutting. The characteristics of the molding compound are: bundled, relatively compact, small specific volume, small feeding chamber of the required mold, simple charging, less fiber damage during the production process, and the molding plastic can be oriented according to the state of the product. High-strength products can be produced, but the fluidity of the molding compound and the mutual compatibility between the bundles are slightly poor, and the production amount is lower than that of the premixing method. The prepreg method can be further divided into a manual method and a mechanical method, and a mechanical prepreg method is generally used in industrial production. Among them, the manual prepreg manual prepreg fiber pretreatment, compounding and drying processes are basically the same as the premixing method, but the fiber length is 600-800mm, no fluff is required, and the relative density of the glue is controlled at 1.00~ Within the range of 1.025. When dipping, a copper rod is used as a scraping roller, and the fiber is pulled by hand through the two copper rods, and the dried prepreg is cut into a desired length and sealed in a plastic bag. The process of the mechanical prepreg method is: the fiber is led out from the creel and passed through the bundle ring into the glue tank dipping. The relative density of the glue is controlled at 1.00~1.025, the fiber pulling speed is 1.2~1.35m/min, and the fiber is dipped by scraping. The rubber roller is dried in the first and second ovens. The first stage oven temperature is 110-120 ° C, and the second-stage oven temperature is 150-160 ° C. The dried prepreg is taken out by the pulling roll into the cutting machine and cut into the required length and sealed in a plastic bag.
The extrusion method uses a screw extruder to produce a glass fiber molding compound. It overcomes the disadvantages of using a large amount of organic solvent in the premixing method and the prepreg method, improves the sanitary condition, reduces the cost, and the product quality is uniform and stable and can be continuously The automatic production has the disadvantage that the fiber is worn and cut in the screw extruder, which is serious and reduces the strength of the product, and is not used in the production of epoxy fiber molding compound.
Zbs Clevise is Link Fitting. Link fitting is used for insulators, Suspension Clamp, clamp and protection fittings connected to form a suspension or tension string set of fittings.
ZBS Clevises are used to attach clevis tongue insulators to various associated hardware within an insulator string.
ZBS Clevise is widely used to connect insulator & insulator, or connect insulator and ground wire clamp to tower arms or subjection structures. The cotter pin are stainless steel, the other parts are hot-dip galvanized steel.
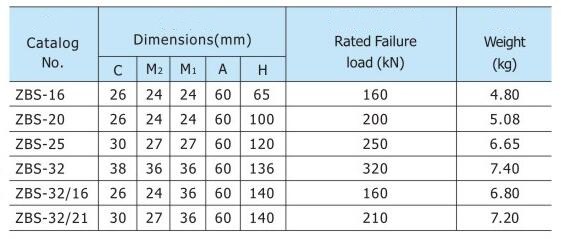
If you have any questions, please contact with us directly.
Our company is solemnly committed to the majority of customers: reasonable price, short production cycle, considerate service. We look forward to cooperating with you.
ZBS Clevise
Zbs Clevise,Zbs Type Clevise,Link Fitting Zbs Clevise,Zbs Clevis For Overhead Line Accessories
Shandong Vantage International Trade Co., Ltd. , https://www.steelplate.be